Hybrid and electric drivelines typically incorporate aluminium castings for housing electric motors and electric drive units. Optimising the performance of the electric motor is dependent on maintaining temperature control, meaning that the castings will often contain complex cooling systems.
We’ve also seen a shift towards the use of aluminium for EV battery housings. To ensure batteries are always kept at the right temperature also requires a cooling system, typically using refrigerant or water glycol. In some next generation battery cases, batteries are immersed in a fluid to control them, using pressure-tight structures.
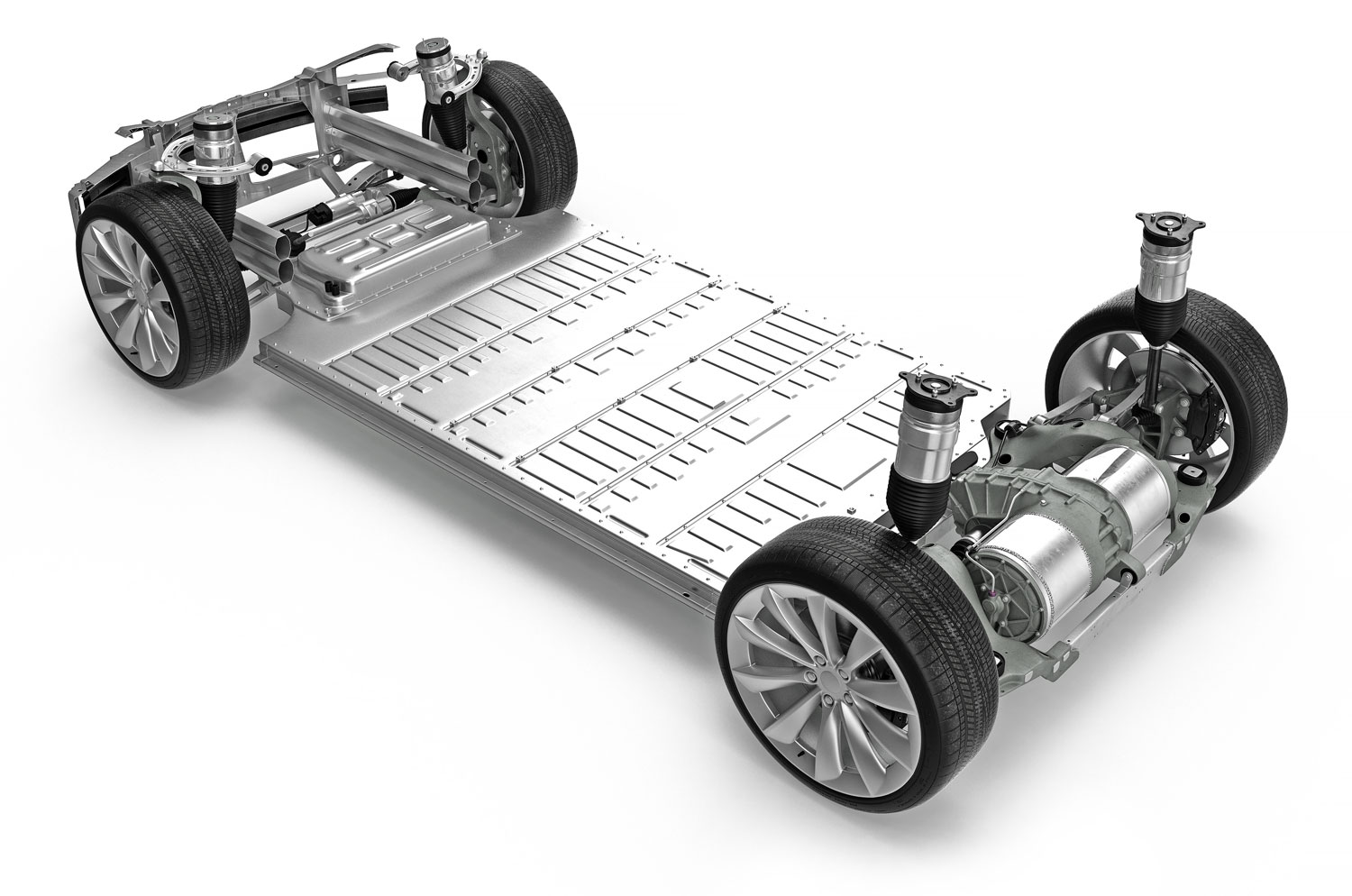
While the emerging electric market looks set to continue to rely on the casting industry, manufacturers must be able to produce complex, light-weight components whilst facing the ever-present pressure to reduce costs and improve productivity.
The inevitable challenge of porosity
An inevitable challenge facing auto manufacturers using light-weight materials for complex components is casting porosity. When porosity causes a leak path in pressure or fluid-tight structures, the part becomes unusable, meaning increased production costs and reduced productivity.
The solution to sealing casting porosity is through a vacuum impregnation process using a thermally and chemically resistant polymer. For the most effective quality enhancement results, the impregnation process is increasingly integrated within the production facility or even in-line with the manufacturing process.
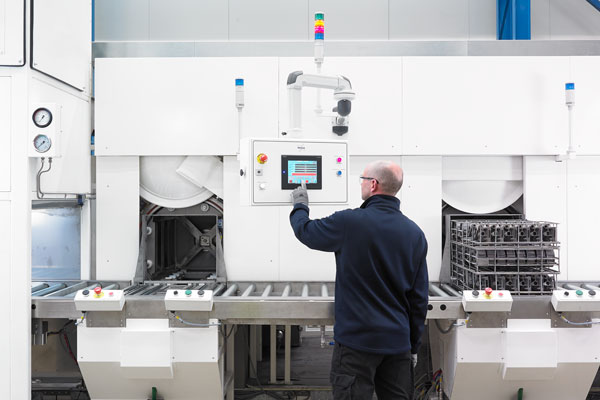
Looking forward
There’s clearly an important role for the casting industry in future vehicle design, but it’s considerably more evolved with ever more sophisticated castings than previously. The manufacturers of electric powertrains will require the extensive knowledge of Ultraseal International, who can bring their expertise to both sealing casting porosity and providing impregnation technology tailored to individual production processing requirements.
To find out more about the unrivalled solutions to sealing porosity provided by Ultraseal, use the links below; or alternatively get in touch with our team.